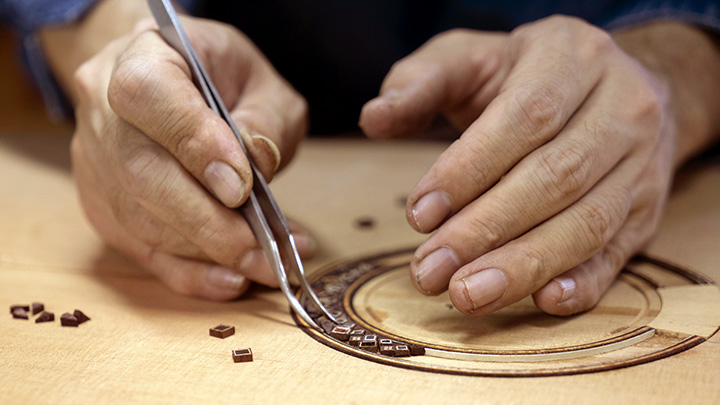
Shin-ichi Fukuda performs Johann Sebastian Bach's "Cello Suite No 1" in our workshop.
The making of a guitar begins with the choice of wood, notably spruce and red cedar for the top and rosewood for the back and sides.
We are always looking for the best wood.
We will personally see, touch, smell and listen to wooden boards from all over the world before choosing them.
Many boards and pieces of wood are carefully stored in our workshop which is now over 70 years old.
Our wooden boards are dried for a period of 10 to 30 years. Some of the boards we keep for experiments or special orders are over 50 years old.
The climate of the Kanto region of Japan, hot and very humid in summer and cold and dry in winter, offers a special opportunity for drying wood. Some wood boards, when exposed to the natural climate of Japan, without climate control, do not stand up, warp and crack. We therefore eliminate inferior woods and use only the most stable woods that are less likely to warp and crack in a changing climate, wherever our guitars are sent. In countries and regions with a more stable climate, this natural drying process makes it more difficult to select good wood boards.
Parts of the guitar where it is difficult to remove water, such as the ebony neck reinforcement and fingerboard material, are dried in an artificial dryer.
After drying, the guitars are made in a room where the temperature and humidity are strictly controlled. The wood is glued with a glue containing water, and a drying period is necessary after each gluing operation. Parts of the guitar where it is difficult to remove water, such as the ebony neck reinforcement, are dried in an artificial dryer.
It's a long maturation process; up to a year between the start of production and the final guitar.
The three types of climate control, natural drying to select stable woods, artificial drying at key locations and managing the stability of the temperature and humidity of the workshop, have brought our guitars worldwide recognition.
The wood is glued with a glue containing water, a drying period is necessary after each gluing operation. It is a long maturing process; up to a year between the start of production and the final guitar. The glue is made from animal bones, hides and sinews that are boiled in water, then dried and hardened.
As the glue ages, it becomes softer and does not interfere with the vibrations of the wood.
The soundboard that produces the sound is usually made of softwood less than 3 mm thick.
The six strings of a classical guitar exert a total tension of more than 40 kg, and if left unreinforced, the soundboard would warp or crack under the tension of the strings. A set of wooden ribs called a bracing is therefore placed under the soundboard to resist the tension of the strings. The construction and thickness of the bracing also allows the sound waves to propagate through the soundboard and has a significant influence on the sound quality of the guitar.
The bracing is therefore fundamental to the strength and sound quality of the guitar. Many guitar makers have tried to solve this problem by strengthening the lower strings, which are heavier and give more energy when played with the fingers, while the higher strings are lighter and produce less sound than the lower strings.
The first guitar bracing in the 18th century was symmetrical but asymmetrical bracing appeared in the 19th century, notably with René François Lacôte (1785-1855) who added a bias rib under the rosette.
This asymmetry allows the vibrating part of the table on the low string side to be enlarged and the part on the high string side to be shortened. The increased stiffness of the top on the treble side gives a richer sound in the treble.
Later, Antonio de Torres (1817-1892) increased the size of the guitar body and opted for a symmetrical fan bracing, which had a major influence on classical guitar design.
The asymmetrical bracing reappeared at the beginning of the 20th century with Santos Hernandez (1874-1943) using an angled rib and Enrique Garcia (1868-1922) using an extra rib on the high string side: 4 on the high string side and 3 ribs on the low string side.
Many luthiers such as Ignacio Fleta (1897-1977), Robert Bouchet (1898-1986) or Daniel Friederich (1932-2020) have experimented with different symmetrical and asymmetrical bracings.
José Ramírez III, Manuel Hernández (1895-1975) and Victoriano Aguado (1897-1982), based on the idea that the low strings are heavier than the high strings and therefore have more action on the table, reinforced their bracing not on the side of the high strings but on that of the low strings.
Robert Bouchet created an asymmetry not by adding a rib at an angle or by the difference in the number of ribs, but by the thickness of the ribs, with ribs less thick in height on the bass side than on the treble side.
Masaru Kohno opened his workshop in 1949 and from the beginning he experimented with new bracing systems, oblique, symmetrical and asymmetrical, with or without a rib under the bridge. However, the first bracing was symmetrical.
After winning in 1967 the gold medal at the Elizabeth's Concourse international guitar making competition in Belgium, Masaru Kohno intensified his experiments in search of a unique sound. A unique and sophisticated bracing system was created by designing the soundboard on the low string side to be more flexible and on the high string side to be more rigid. The new bracing allows for denser, deeper bass tones and clearer, more expansive highs.
From the 1980s onwards, Masaru Kohno designed a new type of bracing (two-way bracing), in which the pieces are surrounded by a double square rib.
Masaru Kohno continued to use this principle until his death in 1998 and the current SAKURAI-KOHNO range is based on the bracing from this period.
Masaki Sakurai, successor of Kohno Guitar Manufacturing, after using Masaru Kohno's bracing, develops his own bracing based on his experience and intuition.
In 2002, a collaboration with Professor Hiroshi Okamura, who specialises in vibration engineering at the Shibaura Institute of Technology, led to a major change. Masaki Sakurai attached sensors to soundboards to study the propagation of sound and analyse the vibration mechanisms.
The result of his research is a bracing running across the top and bottom of the soundboard, instead of a much reduced bracing on the bass side. The result is a richer overall tone, tighter bass without loss of volume, and better defined highs. All MASAKI SAKURAI models are equipped with this system.
So Kimishima, after studying the guitars of Masaru Kohno and the theory of dams and vibrations of Masaki Sakurai, seeks to create a different sound line.
Based on his knowledge of wave propagation and soundboard vibration at each sound frequency and analysis of spectral components, So Kimishima takes a scientific approach to bridge design and experiments with the shape of bridge parts to the best of his ability.
By repeatedly cutting up and dismantling the soundboard and bracing while playing with the strings, he came to understand one by one the influences of the bracing, the shape of the parts and the tension of the strings on the sound. By freely experimenting with some fifty guitar prototypes, he accumulated the experience necessary to combine scientific knowledge and personal sensitivity to create a unique sound.
So Kimishima's current bracing improves the weakness of the high tones, without losing the natural tone and resonance of the guitar, by incorporating a lattice bracing shape only on the periphery of the high side. Compared to the bracing of Masaru Kohno and Masaki Sakurai, the connotations are more discreet. This bracing is positioned as a modern type and is mainly used for red cedar tables.
As he developed his understanding of wood composition, So Kimishima learned how the physical properties of wood change over time and understood the perfection of the fan bracing. Through discussions with guitarists and guitar professionals, So Kimishima also developed a classic spruce top bracing that is simpler and has reduced overtones. Spruce is a denser wood than red cedar, with a slightly harsher sound at first, but as it ages and under the influence of the guitarist, the sound becomes more rounded.
At the moment, both types of bracing, although they have different tones, are well received by guitarists and we receive orders for both types in equal measure.
The varnish not only protects the guitar from environmental changes such as humidity, it is also fundamental to the quality of the sound. An unvarnished guitar will produce a rough sound that is unsuitable for musical expression, but conversely, too thick a varnish will diminish the natural sound quality of the wood.
Our varnishing method consists of creating a very thin film of polyurethane on the wood grain and then spraying a single thin layer of cashew varnish with a spray gun. Three thin layers of polyurethane are applied to the wood and then removed with a scraper and paper, leaving only the interior of the grain. The final, very technical step is to wipe the cashew in one go and cover it with a thin film of varnish, which is then carefully polished with paper to complete the process.
One of the major differences between a mid-range and a high-end guitar is the amount of time spent on the varnish and its fineness.
Cashew nuts
Cashew varnish is made from extracts of the outer shell of cashew nuts (also known as cashew nut). Similar in composition to lacquer, it is also known as artificial lacquer because it has a transparent sheen and gloss similar to lacquer.
Lacquer is sensitive to moisture, whereas cashew is extremely resistant. This varnish also has very high anti-climatic and denaturing properties. It is the softest of all finishing varnishes. The varnish, even when sprayed, does not interfere with sound vibrations and adds brilliance to the tone. It also has a very high viscosity, which avoids the risk of cracking if the wood changes over time.
Kohno Guitar Manufacturing began using cashew nuts in 1960 and continues to use them in all of its guitar lines because they suit the characteristics and sound of our guitars.
Shellac
The classical guitar originated from traditional Spanish craftsmanship and many luthiers believe that the traditional Spanish shellac varnish is the most suitable varnish for classical guitars. Shellac is a lacquer made from the secretion of an Asian cochineal which, when dissolved in a mixture of alcohol, can be used as a varnish. It is believed to be the first varnish used by man.
This varnish, which is harmless to the human body but very sensitive to humidity and human sweat, requires some care.
The shellac-based French polishing method allows the application of very thin layers of varnish and offers a unique visual and sound result.
We are sometimes asked whether a shellac-based buffer varnish is possible on Masaki Sakurai and Sakurai Kohno guitar models. This is not possible, however, because of the design of the solid bracing. A shellac-based varnish would harm the sound of the guitar and a soft finish such as cashew varnish is more appropriate.
The influence of the varnish on the sound of a guitar is very important and the choice of varnish is adapted to the sound production of each manufacturer.
However, shellac, lacquer or cashew varnish finishes are possible for So Kimishima's LUNA and SOL models because the bracing are designed differently.
The type of varnish has no influence on the price of our guitars.
So Kimishima, after studying the structure and characteristics of guitars, incorporates new ideas.
One of the goals is to create a new generation of guitars by incorporating unique innovations that increase the life span of guitars that will accompany musicians throughout their lives.
* The following innovations are currently only incorporated in selected models of the Kimishima range.
Discover the SOL model...
The rosette is an ornament around the circular opening of the soundboard of a guitar.
Like the head of a guitar, the rosette is a piece that each luthier personalizes, like a signature.
There are some very good rosette manufacturers, but in the SOL model, So Kimijima makes its rosettes entirely by hand to achieve complex and unique combinations.
We use the ends of the wood without the addition of dyes; each type of wood is used for its natural colour.
We freely combine 36 species of trees from all over the world and create unique rose patterns.
Depending on your preferences and choices, we can personalise your rosette with a sober or bright design or with your favourite tree species.
From left to right : American holly, white ash, maple, eucalyptus, chestnut, mempisang, satinwood, beech, olive, white oak, cherry, cedar, black cherry, opancor, Hawaiian koa, Haitian blackwood, palo santo, black walnut, ziricote, Honduran mahogany, teak, bubinga, Cuban mahogany, snakewood, paddock, satinwood, redwood, cocobolo, jacarandá, granadillo, Brazilian rosewood, Indian rosewood, Madagascar rosewood, katalox, Kalimantan ebony and African ebony.
In traditional classical guitar making, the top is glued to the sides with small triangular pieces of wood that follow the curve of the sides: the kerfing blocks. This method allows the top to vibrate smoothly and produce a deep, rich sound.
Conventional gluing of the sides is not perfectly adapted to the curves of the sides and, depending on the development of the glue, the humidity and the temperature, peeling problems can occur.
So Kimijima's LUNA and SOL models avoid peeling by embedding the kerfing blocks in the inner part of the double-layer sides. This allows the sides to withstand the vibrations of the soundboard in the vertical direction as well as long term aging. (Other Kono Guitar Manufacturing models use guitar Linings which ensures sufficient adhesive strength).
This new Kerfing blocks technique reduces energy loss and produces a rich, deep sound. In addition, the double-layered sides have a synergistic effect on the transmission of sound to the front and back, and provide sufficient sound performance for large spaces such as concert halls.
If a guitar is used for a long time, the string holes in the nut widen and the angle of the strings on the nut changes; the sound may no longer be produced as intended or there may be noise in the sound.
So Kimishima's LUNA and SOL models have a bone plate embedded in the saddle for strength and to reduce the gap between the string holes.
It is not usual to install a reinforcement bar in the neck of a classical guitar; it has a significant effect on the tone of the guitar and changes the typical sound of classical guitars. However, each piece of wood is unique and the environment in which the guitar is kept varies from user to user, which may result in neck distortion.
There are several ways to create a correct curve in the neck. The hot iron method, where the handle is heated to give the wood the habit of the correct curve, works well to correct small curves, but may not be able to cope with large deformations. In So Kimijima's LUNA and SOL models, a laminate is made by soaking glue on a low density shina wood board and sandwiching it between two pieces of ebony wood, which are then embedded in the handle. This laminate uses the tendency of the "Nikawa" glue to melt when heated and to harden when cooled, making it easier to work the curve of the handle with the hot iron method.
*It is difficult to control the condition of the neck 100% by heat alone, although the effect has been confirmed. In some cases it may be necessary to take measures such as re-fretting or shaving the fingerboard.
When bending tests were carried out under similar conditions on straight and laminated ebony panels, the laminated panels retained two to three times more bending.